The Latest from Western Farm Press
Marijuana farm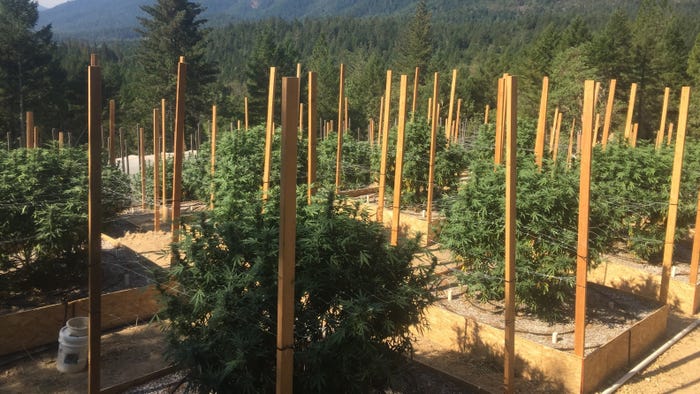
Commentary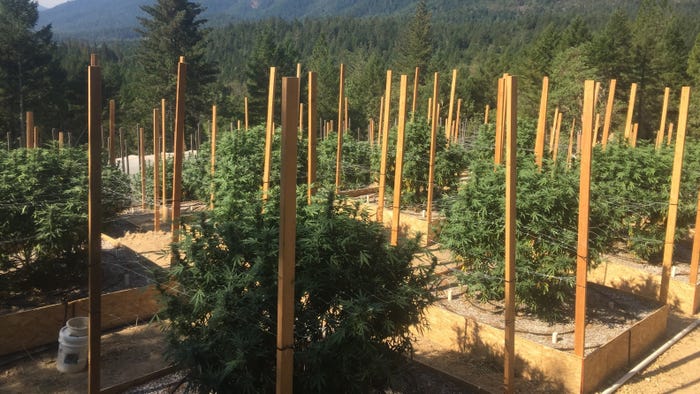
Calif. pot industry owes $732m in taxesCalif. pot industry owes $732m in taxes
Most of it is owed by businesses that have already failed.
Market Overview
Contract | Last | Change | High | Low | Open | Last Trade |
---|---|---|---|---|---|---|
Jul 24 Corn | 449.5 | -2.5 | 454 | 449.25 | 451.75 | 05:54 PM |
Jul 24 Oats | 355.25 | +4.25 | 356.75 | 352.25 | 352.25 | 05:53 PM |
May 24 Class III Milk | 18.03 | -0.15 | 18.4 | 17.72 | 18.28 | 05:53 PM |
Jul 24 Soybean | 1173.75 | -6 | 1181 | 1172.5 | 1179 | 05:54 PM |
Aug 24 Feeder Cattle | 260.575 | +2.275 | 261.55 | 258.35 | 258.9 | 05:54 PM |
May 24 Ethanol Futures | 2.161 | unch — | 2.161 | 2.161 | 2.161 | 09:38 PM |

Copyright © 2019. All market data is provided by Barchart Solutions.
Futures: at least 10 minute delayed. Information is provided ‘as is’ and solely for informational purposes, not for trading purposes or advice.
To see all exchange delays and terms of use, please see disclaimer.
All Western Farm Press
Subscribe to receive top agriculture news
Be informed daily with these free e-newsletters